There are a number of different variants of speedo which have been attached to the mini over the years, not only in position and make, but also in scales and design. The early central speedos were made by Smiths and they had the foresight to actually print the TPM on the face of the clock, normally around the odometer. This is pretty much true for all Smiths clocks of that era. Here's an example
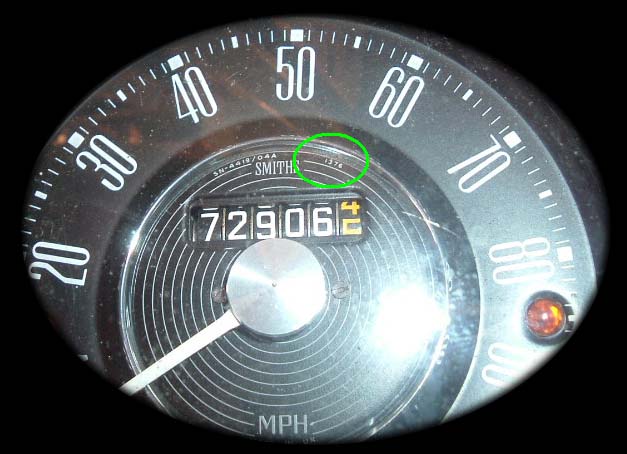
With the introduction of the Clubman came along the dual, and tri, clock arrangement which was housed in front of the driver. These clocks were also made by Smiths and on the early variants these still had the TPM printed on the face of the dial, just a little more inconspicuous. It can bee seen clearly by removing the glass and the facia from the clock, but can also just be made out with the unit together.
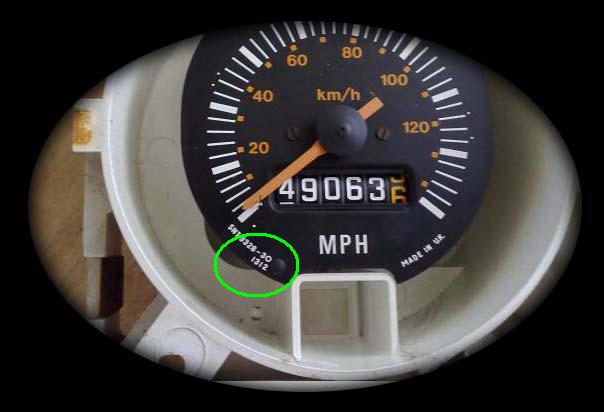
Unfortunately things now get a little more interesting. The internal design of the clocks changed and along with this change the printing of the TPM on the speedo face also seemed to have disappeared. However, on a number of variants, the TPM was introduced as part of the injection moulding for the drive gears in the speedo.
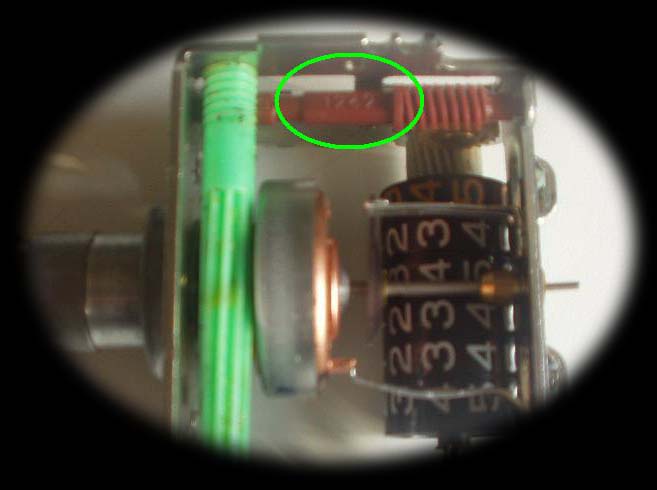
But this is not true for all, and hence the only way to find the TPM of most of the latest speedos is to count teeth. So here's how.
There are 5 main driven parts in the speedometer, The input (A) which is driven by the speedo cable and moves the needle, then a pair of pinion/worm drives (B and C) which act as a reducer and transfer the drive around the speedo cage to the odometer, then what can be best described as a drop gear or idler (D) which transfers the drive to the final drive (E) on the end of the odometer. To work out the TPM of the speedo you need to calculate how many times the input (A) has to turn, to turn the final drive (E) one complete revolution.
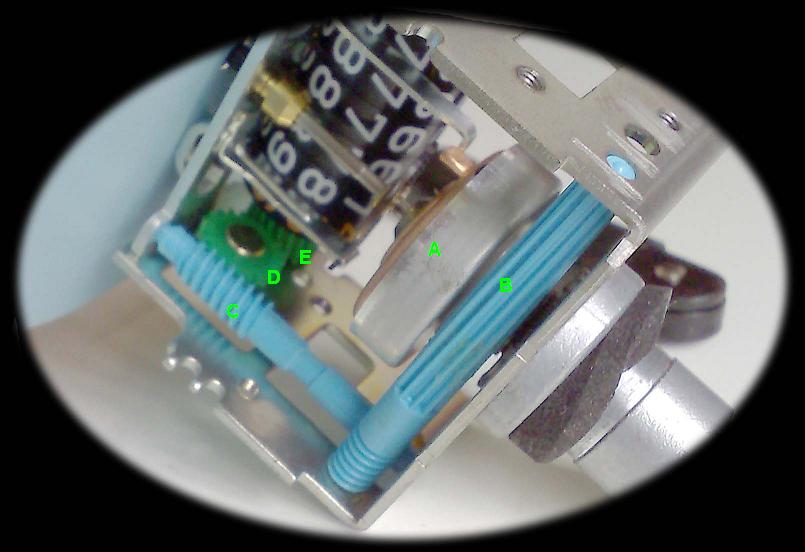
Counting teeth which run parallel to the axle is easy, you just need to count the number of teeth around the gear, but when counting a worm drive you need to count the number of helices (plural of Helix). Most of the time there will only be one (like a screw), but sometimes there are two or even three.
So starting with the main drive (A), there is a worm drive on this which rotates the first of the transfer shafts (B), this only has one helix, so for every rotation of A the shaft B rotates by 1 tooth.
The shaft B has 10 teeth, this was discovered by marking one of the teeth with a felt tip pen, and then using a match stick, the speedo was turned by hand and the teeth counted as shaft B rotated. The point of the mark is to know when to stop counting.
On the other end of shaft B there is a worm drive, so you need to count the helices. In this case there is only one.
Things now get a little more fiddly, the worm on the end of shaft B drives a gear on the end of shaft C, counting the number of teeth on this gear gets a little harder, but can be done by rotating A again with a match stick, but this is time consuming, so with the judicious use of an electric drill, shaft A can be turned at such a speed to make the counting on teeth easier. Use the felt tip pen to mark one of the teeth as before. In this example there are 13 teeth on the gear.
As with shaft B, shaft C has a worm drive on the other end, which drives the transfer gear (D). There are 2 helices on the end of shaft C, which means for every rotation of C the idler D, moves on by 2 teeth.
The number of teeth on D is unimportant as this just acts as a drive transfer to the final drive E, and has no bearing on the ratio calculation to follow.
Finally, you need to count the teeth on gear E, this is really fiddly, so do it a few times to make sure, but if using an electric drill it does not take too long. Use the mark method as before. 20 teeth in this example.
You now have a series of numbers for each part of the drive mechanism (with the exception of D)
So start by dividing the number of teeth on shaft B (10) by the number of helices on A (1), nice easy one to start with, 10/1 = 10.
Divide the number of teeth on shaft C (13) by the number of helices on the end of shaft B (1), 13/1 = 13
Divide the number of teeth on E (20) by the number of helices on the end of shaft C (2), 20/2 = 10
Now the trick; multiply the three given numbers together, 10 x 13 x 10 = 1300.
So this is a 1300 TPM speedo, or the speedo cable has to go round 1300 times for the odometer to register one complete revolution, one mile.
Now treat yourself to a cup of tea and a biscuit as you've deserved it.
Guessworks.